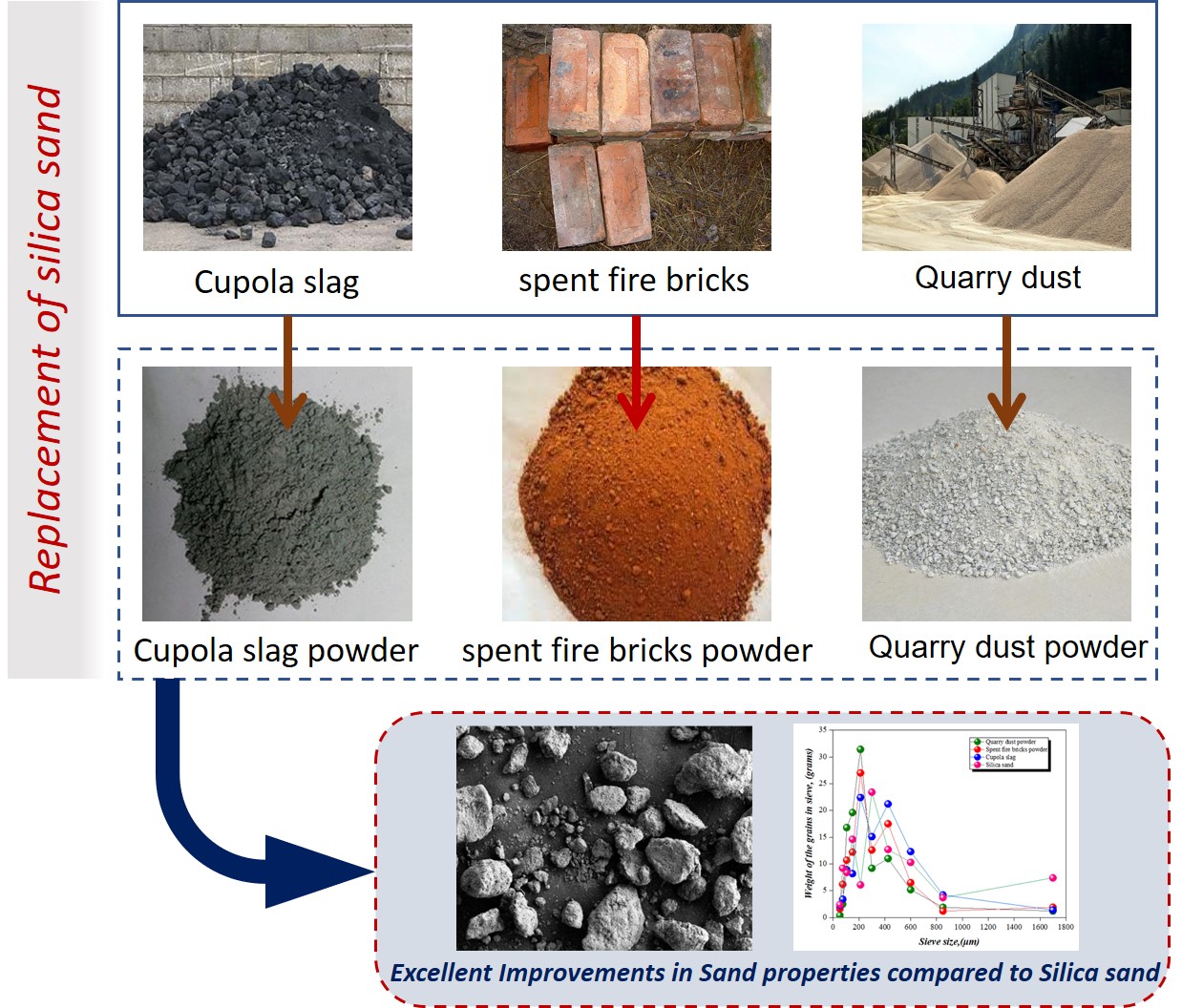
Green sand moulding uses silica sand for metal casting. Silica sand mining and delivery to foundries destroy the ecosystem, making metal casting unsustainable. Due to increased sand-casting output and massive civil buildings in India, the silica sand supply is declining. The depletion and shortage of silica sand necessitate the search for viable replacements. Industrial solid waste from large-scale industrialization pollutes land, air, and water. In order to use industrial waste in large amounts, an attempt is made to use it as a replacement for natural resources. The main objective of this research is to reduce the consumption of silica sand in the foundry mould-making process. Silica sand is replaced with industrial solid waste, cupola slag, and construction solid waste sources like spent fire bricks and quarry dust, up to a considerable amount, to save the natural resources. Utilization of solid waste material in the mould-making process will reduce production costs and environmental pollution, like dumping solid waste materials on land. Sand tests like permeability, green compression strength, dry compression strength, and compactability were conducted to assess the moulding properties of these alternative moulding materials. The process parameters considered for this investigation were the percentage of bentonite binder and the percentage addition of alternative mould materials with silica sand. The various sand tests showed that 40%, 30%, and 20% of quarry dust, spent fire bricks, and cupola slag, respectively, will adequately replace silica sand for mould making. A bentonite binder of 8% is suitable for quarry dust mould, and a 10% bentonite binder is required for spent fire brick particles and cupola slag to yield better results. Aluminium castings were produced at the optimal mixture of these solid waste particles and silica sand. The results of mechanical tests such as hardness, tensile, and impact tests are comparable to those of silica sand castings.
Total file downloads: 6